What is Porosity in Welding: Understanding Its Causes and Enhancing Your Abilities
Porosity in Welding: Identifying Common Issues and Implementing Best Practices for Avoidance
Porosity in welding is a pervasive problem that frequently goes undetected until it creates significant issues with the honesty of welds. In this discussion, we will certainly discover the essential variables contributing to porosity formation, analyze its detrimental effects on weld efficiency, and review the best methods that can be taken on to reduce porosity incident in welding procedures.
Common Sources Of Porosity
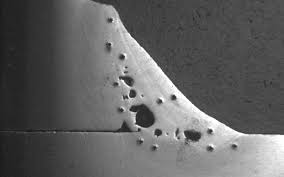
An additional regular culprit behind porosity is the visibility of contaminants on the surface of the base steel, such as oil, grease, or corrosion. When these pollutants are not properly gotten rid of prior to welding, they can vaporize and end up being caught in the weld, causing problems. Additionally, using dirty or wet filler products can present contaminations right into the weld, adding to porosity problems. To mitigate these common reasons of porosity, thorough cleansing of base steels, proper protecting gas selection, and adherence to optimum welding parameters are essential techniques in accomplishing premium, porosity-free welds.
Effect of Porosity on Weld Top Quality

The existence of porosity in welding can considerably endanger the structural honesty and mechanical residential properties of welded joints. Porosity develops voids within the weld steel, deteriorating its overall stamina and load-bearing ability. These spaces work as stress and anxiety concentration factors, making the weld more prone to cracking and failure under used lots. Additionally, porosity can decrease the weld's resistance to rust and other environmental factors, better diminishing its durability and efficiency.
Welds with high porosity levels often tend to show reduced effect strength and reduced capacity to flaw plastically prior to fracturing. Porosity can impede the weld's capacity to efficiently transmit forces, leading to premature weld failing and prospective security dangers in essential frameworks.
Ideal Practices for Porosity Prevention
To enhance the architectural stability and high quality of welded joints, what certain actions can be implemented to reduce the incident of porosity throughout the welding procedure? Making use of the correct welding technique for the particular material being bonded, such as changing the welding angle and weapon position, can additionally stop porosity. Normal inspection of welds and immediate remediation of any issues identified during the welding process are important methods to avoid porosity and create high-grade welds.
Importance of Proper Welding Techniques
Implementing correct welding techniques is vital in ensuring the architectural integrity and high quality of welded joints, constructing upon the foundation of efficient porosity prevention procedures. Excessive warm can lead to increased porosity due to the entrapment of gases in the weld swimming pool. Additionally, utilizing the proper welding parameters, such as voltage, present, and take a trip speed, is critical for accomplishing audio welds with minimal porosity.
Moreover, the choice of welding process, whether it be MIG, TIG, or stick welding, need to align with the certain needs of the job to ensure ideal outcomes. Proper cleaning and prep work of the base steel, as well as choosing the appropriate filler material, are my review here likewise crucial components of skilled welding strategies. By adhering to these finest practices, welders can reduce the danger of porosity development and generate top quality, structurally audio welds.
Testing and Quality Assurance Actions
Quality control procedures play an important duty in confirming the honesty and reliability of welded joints. Checking Visit Website treatments are important to discover and protect against porosity in welding, ensuring the strength and sturdiness of the end product. Non-destructive screening approaches such as ultrasonic screening, radiographic screening, and visual assessment are generally used to recognize possible defects like porosity. These techniques allow for the assessment of weld quality without compromising the integrity of the joint. What is Porosity.
Performing pre-weld and post-weld inspections is also essential in preserving quality control criteria. Pre-weld assessments involve validating the materials, equipment setups, and cleanliness of the workplace to protect against contamination. Post-weld assessments, on the other hand, analyze the last weld for any flaws, including porosity, and validate that it meets defined standards. Applying an extensive quality assurance strategy that includes thorough testing treatments and evaluations is extremely important to minimizing porosity issues and making sure the overall high quality of bonded joints.
Final Thought
In conclusion, porosity in welding can be an usual concern that influences the you could try this out top quality of welds. By identifying the common root causes of porosity and implementing ideal techniques for avoidance, such as proper welding techniques and testing steps, welders can make sure top quality and dependable welds. It is important to focus on avoidance techniques to lessen the event of porosity and keep the honesty of bonded frameworks.